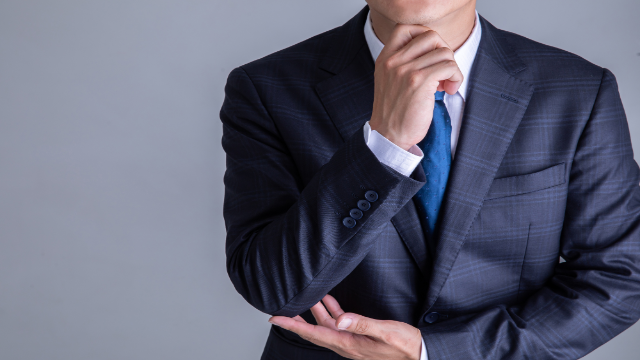
2024.02.28
- お役立ちコラム
深刻化する後継者不足の実態とは?原因と解決策を解説
- 機械事業部
製造業の不良対策の重要性とは。原因を把握して不良の防止を図るには?
2024.05.31
製造業で発生する不良対策に、頭を悩ませている方は多いでしょう。今回は、製造業の不良防止を図るために押さえるべき、不良の主な原因・製造業における不良対策・不良記録の適切な管理の重要性や方法などを解説します。
製造業で不良が発生する主な原因は下記の「4M」です。
・人(Man)
・機械(Machine)
・材料(Material)
・方法(Method)
それぞれの要素がどのように品質不良へとつながっていくかを詳しく解説します。
不良品が発生する原因の中でも、影響度が高いのがヒューマンエラーです。人的要因による品質不良は下記の通り、さまざまな背景から起こり得ます。
・新人が作業になれておらず、手順を間違える
・作業には慣れているが、疲労やモチベーション低下からうっかりミスをする
・現場のコミュニケーション不足で、ミスが見逃されやすい
ヒューマンエラーは、4Mの残りの3つの発生にも関わるため重点的に対策を講じるべき課題です。
製造に使用する機械関係の問題によっても品質不良は発生します。使用設備やジグの変更、製造場所の変更、機械の故障、設備の老朽化、部品の摩耗などが代表例です。
新しく導入した機械の操作方法が従来のものと異なることや、製造場所の変更にともない動線が変わったことなどが不良の原因になります。
ほかにも、整備が十分でない機械の故障が原因で不良が起こることもあります。ただし、定期的にメンテナンスしていても、予期せぬ故障が起こるケースもあります。特に、同じ製造ラインを過度に使っている場合、劣化が早くなるので注意が必要です。
ロットが異なる、材料の製造元が異なるといった場合も品質不良の原因になります。使用する材料の品質が基準を満たしていてもロットが微妙に異なると不良が起こりやすくなるのです。
作業手順が不明確になっていたり、複雑な工程が多かったりすると、製造物の品質不良につながりやすくなります。
また、マニュアルがあっても内容に不備がある、古い情報のままで運用しているといった場合は不良の発生原因になります。
製造業における品質不良の対策を4つ紹介します。
・作業手順書(マニュアル)の作成
・作業環境の整備
・管理の強化
・作業者の指導・訓練
具体的な対策について、詳しくみていきましょう。
作業手順書の作成や既存の作業手順書の見直しは、効果的な製造業の不良対策です。従業員によって工程や作業内容に差が出ると、生産する製品の品質も安定しにくくなるためです。
作業手順書を作成して周知すれば、新人・ベテラン問わず同じ手順で作業を進められる程度に標準化できます。また、すでに作業手順書がある場合でも、正しい情報がわかりやすく書かれているか確認しておくことが大切です。
従業員が作業に専念できるように、製造現場の作業環境を整備しましょう。作業環境が整っていないと、集中力が削がれてミスを誘発し、品質不良が発生する原因になるためです。
具体的には、次のような問題がないか確認しておくことをおすすめします。
・作業や従業員間のコミュニケーションを妨げるような騒音がないか
・まぶしすぎる、暗すぎるといった照明の問題はないか
・寒い、暑いなど不適切な温度になっていないか
・適度に片付いており、取違などのミスを誘発せずに作業できるか
QC工程表などで工程ごとの管理方式を標準化することも効果的です。工程内、工程間における異常を検知できるようになります。
また、「指示や変更点などは、復唱で確認する・図や動画で説明する」といったことをルール化し体制を整えれば、伝達不足によるミスを予防できます。
加えて、定期的に点検・メンテナンスを実施するよう機械の管理体制も強化しましょう。そのほか、従業員で実施するQCサークル活動なども効果的です。
作業者への指導や訓練を定期的に行うことも有効な不良対策です。指導が不足しているときや、作業に慣れてきたときに、ミスは起こりやすいためです。
また、質問しやすい雰囲気づくりも重要です。頻繁にコミュニケーションをとることで、疑問や気付きを共有しやすくなり、モチベーション維持にもつながります。労働災害を予防する観点での効果も見込めます。
製造業においては、不良記録の適切な管理も重要な不良対策です。ここでは不良記録が必要な理由・残すべき情報・管理の課題について解説します。
不良記録は、品質不良の再発を防止するとともに発生した不良による影響を最小限に抑えるために必要です。
不良記録を作成すると、品質不良の詳細を関係者へ速やかに伝達できます。その結果、対応策や再発防止策の決定、顧客の信頼回復に向けた対応をスムーズに実施できるようになります。
記録があれば、的確に品質管理体制の向上に向けた施策が打てるので、製造における効率化や資材のロス削減につながるでしょう。
不良記録に必要な情報は下記の6点です。
1.不良の状況 |
・不良発見日 ・不良発見状況 ・不良発生場所(○○工場○○ラインなど)
|
2.不良の概要 | ・シンプルにわかりやすく概要を記載 |
3.不良の詳細 | ・具体的にわかりやすく記載 |
4.不良の原因 |
・原因と変化点の確認 ・4M:作業員(Man)・設備(Machine)・材料(Material)・製造方法(Method) ・3H:初めて・変更・久しぶり ・根本原因:不良が発生した場合における表面的な原因ではなく、その背後にある根本的な原因(5Whyや特定要因図などを利用して分析する)
|
5.対策 |
・暫定対策 ・根本対策
|
6.対策効果確認 | ・具体的にわかりやすく記載 |
多くの企業が採用する紙の不良記録は、検索性が低いため情報を見返しにくく、対策が後回しになり再発防止に活用しにくいことがあります。
例えば、不良対策の状況が見えにくいことが原因で対策を実行するまでに時間がかかります。対策が不十分なまま製造を続け、不良の再発が発生してユーザーからの信頼が下がり、注文が減少するといったことが考えられます。
不良に対して適切に対策することにより、ユーザーからの信頼低下や収益減少、無駄な出費の削減を実現可能です。そのため、迅速な対応を可能とし、何が問題かを可視化する管理体制が大切になります。
製造業に求められる品質基準は、上がることはあっても下がることはありません。今後、製造記録や不良記録の管理状況や改善への取り組みに関する監査は、ますます増えていくでしょう。クライアントの求める水準を満たし、安心して仕事を依頼できる企業だと思ってもらうことが大切です。
「ゲンバト」なら、図面管理から不良記録・設備管理まで、紐づけて管理可能です。不良の発生から対策実施の状況が一目でわかる上に、情報が自動でグラフ化されることで現状を見える化できます。図面と不良が紐づいて製品ごとに発生した不良の内容を確認でき、設備の管理も厳格化できます。
オリジナルサービスは、2024年12月末日まで無料でお試し可能で、導入支援も充実しています。製造業の効率化を検討している企業は、ぜひお試しください。